天然石墨分选提纯及应用进展概述
作为战略性非金属矿产资源, 天然石墨独特的结构使得它具有良好的导电性(电阻率 8×10−6 ~13×10−6 Ω·m)、可 塑性强、摩擦系数小(0.08~0.16)、耐高温、化学性质稳定、天然可浮性好等物化特性,是多种工业必需的关键原料。同时天然石墨具有用途广泛,深加工产品附加值高,产业链条长等特点,除广泛应用于耐火材料、密封、铸造、导电材料等传统 工业领域,在新能源、新一代电子信息技术、新能源汽车、高端装备制造业等新兴领域也有着极大的应用前景,被誉为“工 业黑金”。我国石墨资源丰富,但尚未成为石墨资源强国,本文对天然石墨分选工艺、提纯方法、深加工产品的制 备及在新兴战略性产业领域的应用展开讨论,系统介绍了石墨资源的综合利用进展,其中主要涉及石墨层间化合物、球形石 墨和石墨烯三类重要的石墨深加工产品。最后,基于石墨产业的发展趋势,给出加强石墨资源开发利用的发展方向。
石墨为多键型晶体,具有层状晶体结构,其层内碳原子与周围3个碳原子通过sp 2杂化形成共价键,构 成类似蜂巢的环状结构;层间以分子间作用力(范德华力)相连接,结合力较弱;层内每个碳原子剩余的 一个具有活性的P电子则形成类似于金属键自由电子模型的离域大π键,因此石墨晶体结构中,既有共价键、 分子键,亦有金属键[1]。独特的结构决定了石墨的物化特性,因其结构中的化学键,石墨具有较强的导热 性、耐热性、化学稳定性;石墨具有优良导的电性则是因其具有离域大π键;特殊的层状结构在外力作用 下容易产生片层之间的滑动,致使石墨有良好的润滑性;同时石墨具有良好的天然可浮性,其接触角θ一 般为85°~86°,疏水性好,经浮选分离可以得到固定碳含量90%以上的石墨。石墨一系列优良的物化性能,使其广泛应用于材料、冶金、机械、电气、环境、化工、国防工业等诸 多领域,是当今世界高新技术发展不可或缺的非金属材料,具有不可复制性和不可替代性,因此许多发达 国家将石墨列为本国的战略性矿产资源予以保护。石墨一直以来也是我国重要的非金属矿产资源,早在 3000多年前的商代就有用石墨书写的文字,为了国家经济持续发展、高效开发利用石墨资源,我国也将晶 质石墨列入战略性矿产资源给予保护。
天然石墨常会伴有各种杂质,难以被直接利用,为了满足工业生产的要求,必须对天然石墨进行富集、 提纯,且石墨纯度愈高其价值也越高。目前关于石墨的提纯方法主要有三种:浮选法、化学法和高温法, 其中化学法又包含碱熔酸浸法、氢氟酸法、混酸法、氯化焙烧法四种。
浮选法
天然石墨具有良好的可浮性,在对天然石墨进行分选提纯时,浮选通常作为第一步使用的方法。现阶段工业生产中基本上所有的天然石墨均采用浮选来进行分选,选矿技术采用多段磨矿、多段选别 的工艺流程,并在此基础上, 针对不同性质的矿石研究更有效、更合理的设备及流程,从而最大限度地提 高固定碳含量和保护石墨鳞片结构。目前,对黑龙江某晶质石墨矿进行层压粉碎-分质分选试验研 究,最终得到固定碳含量为 94.50%的精矿,且其中+0.147 mm 粒级的大鳞片分布率达到 31.24%。对内蒙古某鳞片石墨进行层压粉碎-分质分选试验研究,最终得到固定碳含量为 94.52%的高碳精矿。两 者均证实,将高压辊磨机替代传统工艺中细碎和粗磨设备,能更好的保护鳞片石墨在粗磨阶段的晶体结构, 提高破碎效率,缩短工艺流程,降低能耗。同时也验证了采用不同分质产品的特性分别制定再磨再选的分 质分选工艺流程,可以更有效的保护石墨中的大鳞片,提高浮选效率。浮选法作为石墨提纯的第一步,具有工艺流程成熟、设备简单、能耗少、生产成本低等优点,使其具 有明显的成本优势,但浮选法对石墨的提纯能力有限,无法将部分浸染在石墨鳞片中的夹杂去除,提纯后的石墨固定碳含量很难超过 95%,所以为了得到高纯石墨,必须采取化学法和高温法来进一步对石墨进行 提纯。
化学法
化学法提纯依据石墨化学性质的稳定性,利用强酸、强碱或其他化合物在一定条件下处理浮选石墨精 矿, 通过溶解其中的杂质, 除去杂质,提纯石墨。化学法主要包括以下几种:
碱熔酸浸法
碱熔酸浸法是利用石墨中的杂质在 500℃以上的高温下与 NaOH 起反应,一部分杂质(硅酸盐等)生 成溶于水的反应产物,被水浸出洗涤除去;另一部分杂质(Al2O3、Fe2O3、MgO、CaO 等金属氧化物), 在碱熔后生成不溶于水的沉淀物,经盐酸中和生成溶于水的氯化物,通过清水洗涤而去除。碱熔酸浸法提 纯石墨工艺流程如图 5 所示,此工艺在我国石墨提纯的工业生产中应用最为广泛,随着石墨提纯产业的不 断发展,更为合理、有效的设备及流程也相继出现。

图 5 碱熔酸浸法提纯石墨的工艺流程 目前,刘玉海等[4]利用碱熔酸浸法提纯黑龙江某地细鳞片石墨时,通过探讨适宜的工艺参数,由碱熔 焙烧-水浸出-酸浸的工艺将石墨固定碳含量由 95.89%提升至 99.94%。刘长青等[5]以嵌布粒度较细的隐晶 质石墨原料为研究对象,通过研究隐晶质石墨在不同碱熔条件和酸浸条件下的提纯效果,最终将固定碳含 量为 82.67%的原料,提升至固定碳含量为 93.42%的高纯度石墨,证明了碱熔酸浸法可以有效地提高隐晶 质石墨的品位。碱熔酸浸法是我国石墨提纯产业中应用最为广泛的方法,它具有一次性投资少、石墨碳含量高等特点, 经碱熔酸浸法提纯的石墨固定碳含量可达 99%以上,但想得到 99.9%的固定碳含量则比较困难。同时该方 法大量使用酸碱溶液,容易腐蚀设备,产生的废水污染严重。
氢氟酸法
氢氟酸法是利用石墨中的杂质和氢氟酸发生反应,一部分杂质(Na2O、K2O、Al2O3 等)生成溶于水 的化合物,随溶液排除;另一部分杂质(CaSiO3、CaO、MgO、Fe2O3 等)与 HF 反应生成不溶于水的化合 物,通过加入 H2SiF6 使其生成溶于水的氟硅酸盐,通过清水洗涤,将杂质溶液与石墨固液分离, 从而提纯 石墨。氢氟酸法提纯石墨工艺流程如图 6 所示,该方法具有流程简单,除杂效率高,且 HF 酸对高纯石墨 的性能影响很小,可获得含碳量很高、性能优异的石墨产品。但氢氟酸或 HF 气体有剧毒,对设备腐蚀性 大,对环境污染也很严重,使其应用受到限制,在我国采用此方法的企业并不多。

图氢氟酸法提纯石墨工艺流程 罗伯特·劳埃德等[6]用 HF+H2SiF6 的氟基酸溶液提纯石墨, 使其中的金属氧化物变为可溶于该溶液的氟 硅酸盐和氟化物,并在 70~140 ℃(最好为 130 ℃)的温度下干燥经洗涤处理的石墨,并将已处理的石墨 加热至 250~400 ℃(最好为 300 ℃)以去除石墨中存留的 HF 和 SiF4,得到很好的实验结果。
混酸法
氢氟酸法对环境有较大的污染,提纯石墨过程中,为了减少氢氟酸的使用,往往配合其他酸一起使用, 形成混酸体系。通过混酸体系对石墨进行提纯的方法称之为混酸法,其基本原理同氢氟酸法类似。工业生 产中,主要采用 HF/HCl、HF/H2SO4、HF/HCl/H2SO4 等混酸体系,生产中先后将 HF、H2SO4、HCl 加入石墨中,每加入一种酸后都要充分搅拌,使其能够混合均匀且反应完全。反应完毕后,用工业清洁水反复清 洗,直至中性;再用纯水清洗 2~5 遍;最后进行脱水、干燥、包装。混酸法可以用来生产含碳量为 99.9%以上的高纯石墨。相较于氢氟酸法,混酸法减少了 HF 的用量, 降低了对环境的污染,节省了生产成本。将 HF/H2SO4 混酸法提纯石墨的体系引入热活化作用, 在酸固比为 3:1,700 ℃的温度下,活化 1h,可将原料固定碳含量由 86.42%提高至 99.98%,并且氢氟酸 用量减少了 2/3。王光民[8]在工业生产过程中使用 HF/HCl/H2SO4 混酸法处理固定碳含量为 98%~99%的石墨 时,在 HF、HCl、H2SO4 用量分别为 0.5~0.8 kg、0.4~0.9 kg、0.4~0.7 kg 的条件下,常温反应 24 h,制备 出固定碳含量达到 99.96%的高纯石墨。
氯化焙烧法
氯化焙烧法是将石墨中加入一定量的还原剂(如:焦炭),在一定温度(1000 ℃以上)和特定气氛条 件下, 通入氯气进行氯化焙烧,使石墨中的有价金属杂质转变为熔沸点较低的氯化物或络合物而逸出, 从 而达到提纯石墨的目的。氯化焙烧原理装置示意图如图 所示,
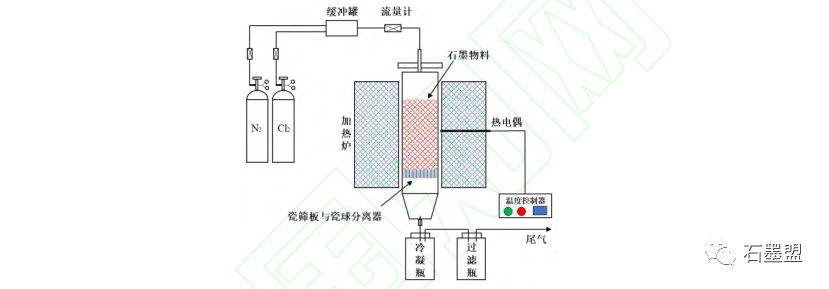
该方法具有能耗低、提纯效率高等优点。但同时设备复杂,工艺稳定性不好,所用的氯气有毒,对环境污染比较严重,产品固定碳含量有限(98% 左右)等诸多不利因素限制了氯化焙烧工艺的应用与推广,该方法仍有待进一步改进和完善。图 7 氯化焙烧原理装置示意图 李继业等[9]在对天然细鳞片石墨进行提纯时,在反应温度为 1200 ℃,反应时间为 2.5 h 条件下,用氯 化焙烧法将石墨碳含量由 86.09%提升至 98.76%。夏云凯[10]在实验室研究的基础上,采用氯化焙烧法对柳 毛某石墨进行中试提纯时,在反应温度 1100 ℃,反应时间 2.5 h,Cl2 压力为 0.05 MPa 的条件下,将原料 碳含量由 88.75%提纯至 99.54%。
高温法
根据加热源的不同,高温法又可分为电阻加热提纯、感应加热提纯、等离子加热提纯、射频加热提纯、 光能加热提纯以及微波加热提纯等六种方法,其基本原理都是依据石墨远高于其所含杂质的熔沸点,在高 温条件下实现石墨与杂质的分离来提纯石墨,最终可以得到含碳量为 99.99%以上的高纯石墨。张向军等通过高温法对碳含量达 99%以上的石墨进行提纯时,经过对实验条件的初步探讨,得到固 定碳含量高于 99.99%的高纯石墨,若通过进一步改善升温工艺条件,提高坩埚质量,可将石墨碳含量提高 至 99.995%以上。
工业应用上,2015 年鸡西浩市新能源材料有限公司采用高温法提纯石墨,运用国内单 体最大的艾奇逊电炉加热到 3100 ℃进行高温提纯,得到碳含量高达 99.99952%的高纯石墨,达到国际先进 水平。相较于其他提纯方法,高温法提纯石墨能够获得碳含量高于 99.99%的高纯石墨,甚至可达 99.995%以 上,但同时该方法对原料纯度、物料细度及设备工艺的要求较高,能耗高,所需投资巨大,因此,该方法 目前的运用领域有限,主要应用于对石墨质量要求很高的航空航天、国防及核工业等特殊领域。
(信息来源:化工进展,天然石墨分选提纯及应用进展概述,作者:郭润楠,李文博,韩跃新)