经常被废弃的铝矾土尾矿如何重新利用生产粘土砖?
铝土矿尾矿是一种典型的工业固体废弃物,大量堆积是对土地资源的占用。此外,尾矿中的废液还会渗入土壤和水域、细颗粒物扬尘污染大气,严重影响当地的生态环境。铝土矿尾矿中含有大量的铝、硅资源(约占总质量的70%),若能开发相应工艺进行合理利用既可以避免环境污染又可以实现资源的再利用。
莫来石是一种优质的高温耐火材料,耐火温度高达1800℃,因其较高的硬度、热震稳定性、抗腐蚀等性能而广泛应用于各种冶炼窑炉。莫来石的化学成分与铝土矿尾矿十分契合,因此近年来大量的研究报道了利用铝土矿尾矿制备莫来石的工艺探索,然而大部分的研究主要偏重于对合成工艺的探讨,针对铝土矿尾矿中Fe2O3、TiO2、CaO、Na2O、K2O等杂质含量对利用铝土矿尾矿制备的莫来石耐火材料的影响研究很少。王金相等研究了K2O和Fe2O3对水铝石-高岭石类型(D-K型)高铝矾土烧结后物相组成的影响,他们发现Fe2O3除了影响制备的耐火材料的白度外,还会增加玻璃相的产生,K2O主要影响莫来石的结晶行为,降低晶相占比。然而这些研究也只是集中在对单一杂质造成的影响,并未考虑多种杂质共同的影响作用。
传统的铝土矿尾矿除杂方法包括物理法(磁选、浮选),化学法(盐酸法、氯化法),生物法等。Kuys.K等研究用盐酸除去极细粒铝土矿(<2μm)中的铁。Fe2O3含量可从5.1%降到1.7%,研究同时指出,三水铝石、一水软铝石、高岭石晶格中的取代铁不能用盐酸除掉。Szabo等在600-850℃下对匈牙利铝土矿进行氯化除铁。Fe2O3含量从16.8%下降到3-3.5%。用差热分析法、X-射线衍射法、穆斯堡尔谱进行氯化除铁机理分析指出,只有铝土矿中的赤铁矿、针铁矿与氯气反应。活化焙烧加酸法除杂是先通过加热焙烧打破尾矿中部分原有矿物的结合形式,提高其在酸浸条件下的活性,再利用酸浸法对焙烧后的尾矿进行除杂,提高除杂效率。这其中盐酸的浓度、酸与尾矿的液固比等是限制除杂效率的关键因素。
本文主要考察以铝土矿尾矿为原料合成刚玉-莫来石基复相耐火材料,通过研究酸浸除杂过程中的盐酸浓度及液固比,得到不同Fe2O3与K2O杂质含量的精矿,对得到的精矿进行烧结制得不同二元杂质含量的刚玉-莫来石基耐火材料,考察不同二元杂质含量对烧结制品性能的影响,并期望在满足使用性能前提下,尽量降低酸浸过程中的盐酸浓度及液固比,降低酸浸对环境造成的影响,优化酸浸除杂工艺。
1实验
1.1实验原料
实验所用的铝土矿尾矿来自中国河南省郑州市,盐酸作为酸浸试剂、聚乙烯醇作为烧结用粘结剂全部购自国药化学试剂北京有限公司。将铝土矿尾矿破碎研磨成细粉利用X射线衍射仪和X射线荧光光谱仪进行物相和成分分析。图1给出了铝土矿尾矿的主要物相组成,可以看出该类型的铝土矿尾矿主要由一水硬铝石(Disapore)、高岭石(Kaolin)、伊利石(illite)、赤铁矿(Hematite)、锐钛矿(Anatase)和石英(quartz)组成。
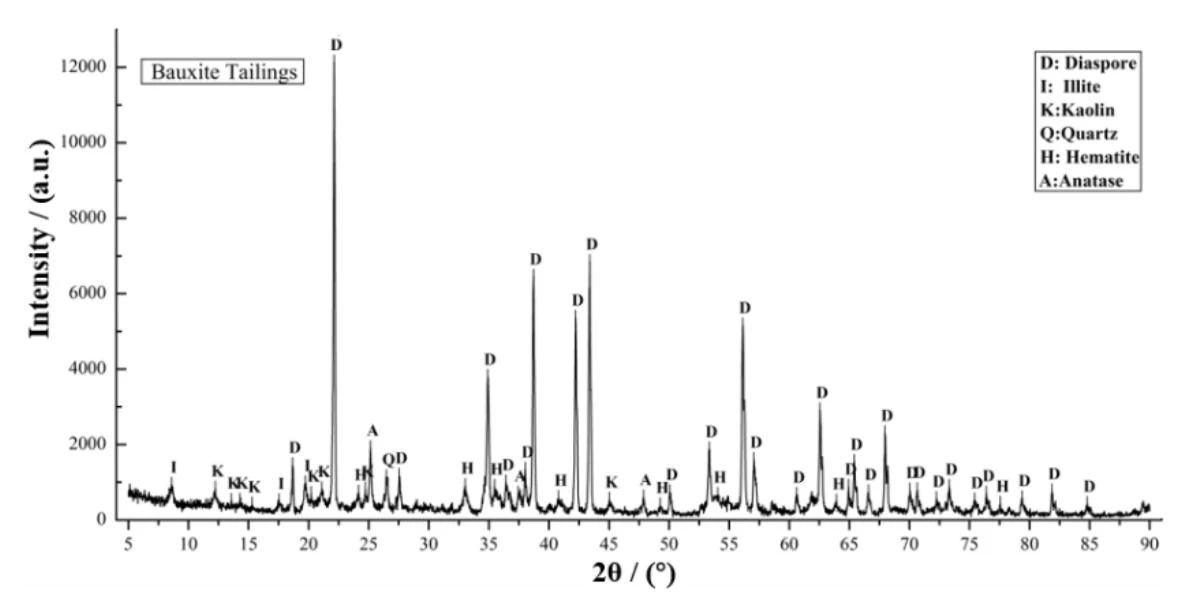
图1铝土矿尾矿的XRD图谱
表1给出了铝土矿尾矿的化学成分,铝土矿尾矿的烧失量为11.5%左右,这部分烧失主要是由吸附水,结晶水,结构水及有机物的挥发等造成的。铝土矿尾矿中的化学含量大于1.0%的主要化学成分有,Al2O3,SiO2,Fe2O3,TiO2及K2O,5种氧化物的含量之和达到了86.92%左右。
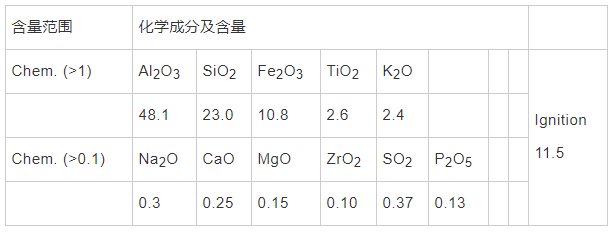
表1铝土矿尾矿的化学成分
1.2 实验设计
首先将铝土矿尾矿细粉在700℃进行活化焙烧,完成尾矿中的一水硬铝石、高岭石与伊利石的脱羟基反应。再将活化焙烧后的尾矿细粉以不同的液固比和盐酸浓度在100℃下进行酸浸除杂2h,具体的实验配比如表2所示。将酸浸后得到的精矿搭配聚乙烯醇作为粘结剂,制成长约60mm,宽约18mm,高约10~12mm的条样,在1500℃进行烧结制备得到刚玉-莫来石基耐火材料。
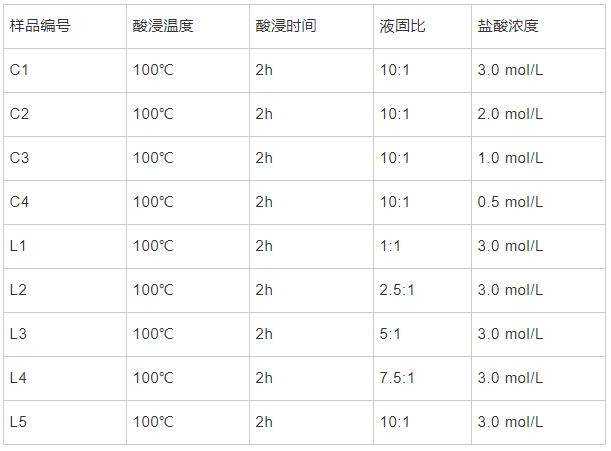
表2铝土矿尾矿酸浸实验设计方案
1.3 材料表征
对烧结样条的矿物组成采用X射线衍射(Xraydiffraction)作为分析手段,仪器型号为(RigakuDmax-2500diffractmeter,Rigakucompany,Japan)。烧结制品的化学成分由X射线荧光光谱(XRayFluorescence)分析法测定,仪器型号为(SEA1000S/A,NSKLT,Japan),烧结制品的化学成分的最终分析结果以氧化物形式给出。显微形貌分析及元素分布分析采用电子扫描显微镜,仪器型号为:MLA250-FEIQuanta。常温抗折及抗压强度的测试设备为:WDW-200微机控制电子式万能材料试验机。荷重软化温度的测试设备为:YB-Zr200A荷重软化测试仪。
2结果与讨论
2.1不同酸浸条件下得到样条中的杂质含量
不同的盐酸浓度和液固比对原料化学成分的影响非常大。表3给出了经过不同酸浸条件后得到的精矿粉的化学成分。图2给出了不同酸浸条件对样条中杂质Fe2O3与K2O的影响。从图中可以看出烧结样条中的二元杂质Fe2O3及K2O的含量随着盐酸浓度的降低而呈现不同的变化趋势,K2O含量从1.62%增至2.11%,平缓增长;Fe2O3随盐酸浓度降低增加明显,尤其在盐酸浓度由2mol/L降到1mol/L时,Fe2O3含量陡增至12.15%。随着液固比升高,杂质K2O含量缓慢下降,而Fe2O3含量随着液固比增加先呈现明显下降趋势,而后逐渐趋于平缓。因此可以得出二元杂质Fe2O3及K2O表现出不同的浸出行为,改变盐酸浓度或者液固比对K2O的影响不大,而杂质Fe2O3则需要较高的盐酸浓度或者液固比实现有效浸出。
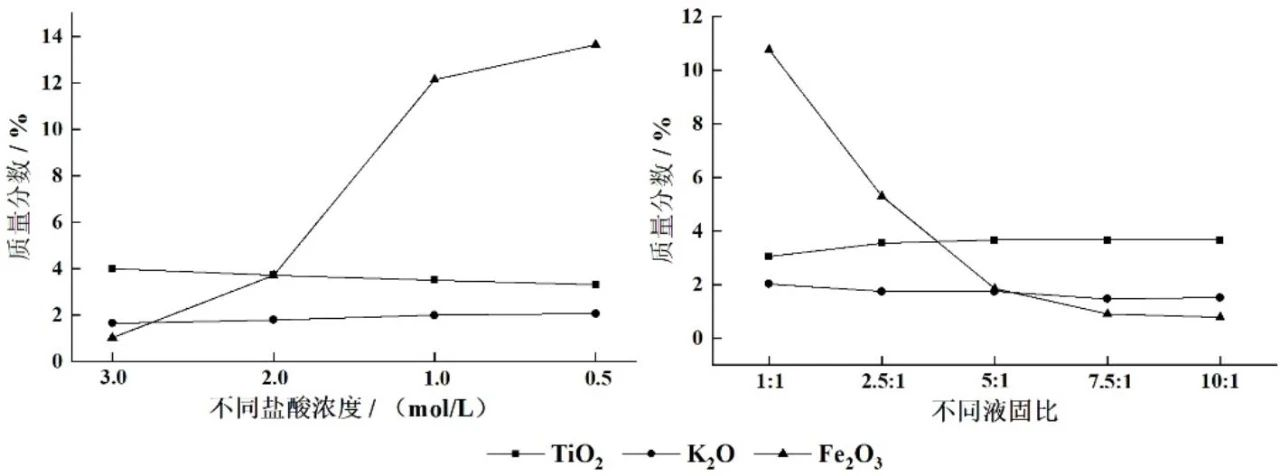
图2不同盐酸浓度与液固比对烧结样条中杂质化学成分的影响规律
表3铝土尾矿酸浸后得到的精矿经烧结后得到的样条的化学成分
2.2 不同酸浸条件下烧结样条的物相组成
上面的分析可以得到不同的酸浸条件对应着Fe2O3和K2O的不同二元杂质组合。图3给出了不同酸浸条件下烧结样条的物相变化情况,可以看出当盐酸浓度大于1mol/L、或者酸浸液固比在2.5:1以上时,烧结样条中的晶相主要为刚玉相、莫来石相与金红石相。反之,烧结样条中的结晶相主要是刚玉相、少量的莫来石相,并有赤铁矿相产生。根据XRD测试结果可以大致估算出烧结样条中莫来石相的占比,结果发现,当烧结样条中的Fe2O3及K2O含量保持在2.0%以下,莫来石相的相对比例保持在30.0%以上。反之,莫来石相的比例将小于30.0%,并且随着杂质含量的提高,这一比例保持下降趋势。
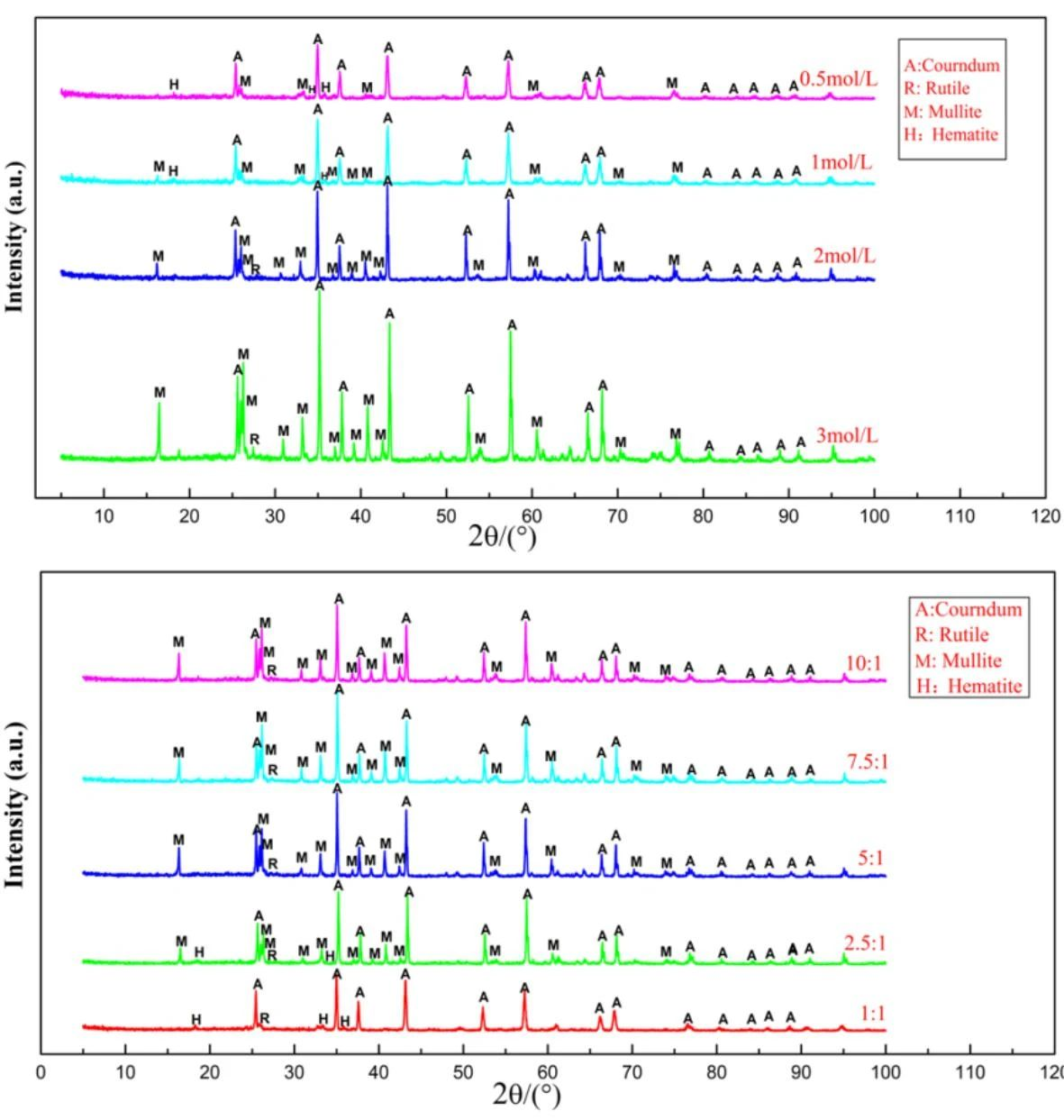
图3不同酸浸条件下得到的精矿烧结条样的XRD图谱
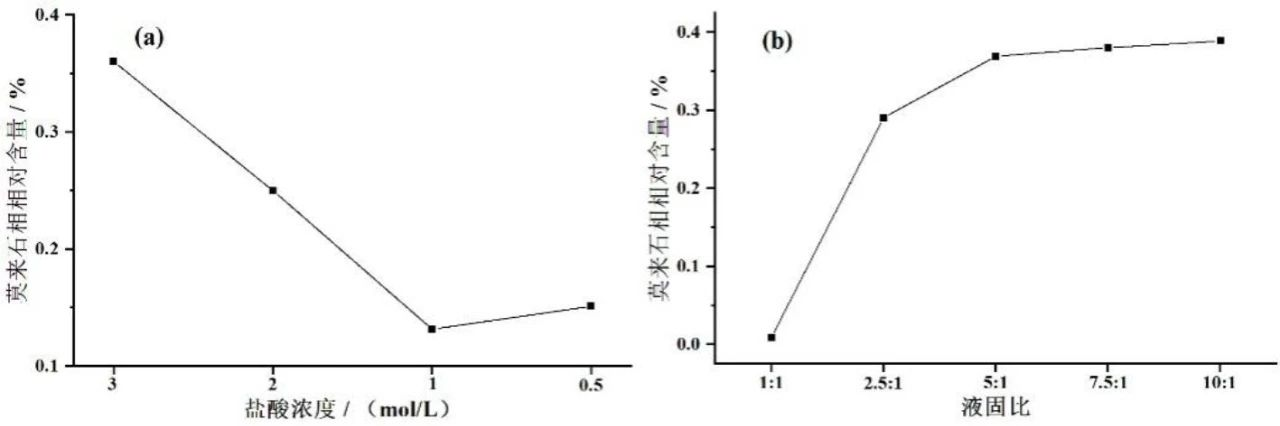
图4不同酸浸条件下烧结条样中莫来石的相对含量:(a)盐酸浓度,(b)液固比
2.3 杂质相对烧结样条微观形貌的影响
不同的二元杂质含量,特别是Fe2O3含量对烧结样条中莫来石的相对含量,结晶相与非晶相的相对比例及非晶相的生成有重要的影响,不同二元杂质含量对烧结样条显微形貌的影响如图5和图6所示。根据图5(a),图6(c)、(d)、(e)可知,在二元杂质Fe2O3及K2O含量均小于2.0%时,图7给出了烧结样条的EDS能谱结果,结合材料的显微形貌可以看出材料由刚玉颗粒相、棒状莫来石相及一定量的非晶相组成,晶相比例大;根据图4(b)、(c)及图5(a)、(b),当K2O含量小幅增加,而杂质Fe2O3提高至2.0%以上时,材料中的棒状莫来石晶相的数量逐渐减少,非晶相的含量明显增加,非晶相对晶相的包裹持续加剧,直至难以区分。这与之前的分析是一致的,说明二元杂质Fe2O3及K2O含量均大于2.0%时,Fe2O3含量的迅速速增加会造成材料中非晶相比重升高,晶相减少。
图5不同盐酸浓度下材料的SEM图谱(a)3mol/L(b)2mol/L(c)1mol/L
图6不同液固比条件下材料的SEM图谱(a)1:1(b)2.5:1(c)5:1(d)7.5:1(e)10:1
图7烧结样条的EDX能谱表征
2.4 杂质含量对材料力学性能的影响
不同Fe2O3及K2O含量样条的抗压及抗弯强度测试结果如图8与图9所示。图中可以看出,在Fe2O3及K2O含量小于2.0%时(盐酸浓度3mol/L,液固比大于2.5:1),材料的抗压强度一般小于15.0MPa,而抗弯强度低于11.0MPa;当Fe2O3及K2O含量均大于2.0%,且Fe2O3的含量大幅增加时,材料的抗压及抗弯强度均大幅提高,抗压强度一般在15.0MPa以上,当Fe2O3含量达到10%以上时候,抗压强度甚至达到90.0MPa以上,抗弯强度达到30MPa以上。材料的抗压及抗弯性能主要决定于材料中晶相与非晶相的相对含量、晶相之间的结合程度和烧结程度。一般的,材料中晶相的含量越高,晶相之间结合的越紧密,烧结强度越高,抗压及抗弯强度越高。而对于测试样条,当Fe2O3及K2O含量均小于2.0%时,根据之前的分析,材料中晶相的含量相对较高,但此时材料的抗压抗弯强度却相对较低,这说明材料晶相间的结合程度较为脆弱,而当Fe2O3及K2O含量均大于2.0%,且Fe2O3含量大幅增加时,虽然材料中晶相的含量大幅减少,但烧结程度大幅提高,材料更为致密(这一点SEM结果可以看出),由此造成材料的抗压及抗弯强度大幅提高。这说明,由尾矿制备的杂质含量较高的刚玉-莫来石基复相材料的常温力学性能高于低杂质含量的样条。
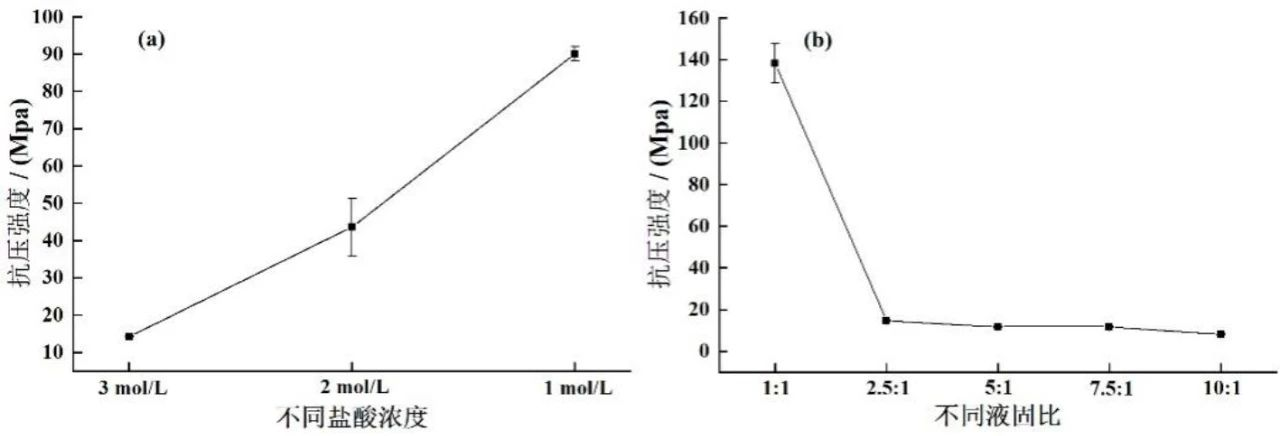
图8不同条件下样条抗压强度,(a)不同盐酸浓度;(b)不同液固比

图9不同条件对样条抗弯强度的影响,(a)不同盐酸浓度;(b)不同液固比
2.5 不同杂质含量样条的荷重软化温度
不同二元杂质含量样条的荷重软化温度测试结果如图10所示,据图可以看出,二元杂质含量的不同对样条的荷重软化温度有非常明显的影响。随着酸浸液固比的降低、试样中杂质含量的增加,起始软化温度逐步下降。当液固比为10:1、7.5:1、及5:1时,起始软化温度分别为1430℃左右、1410℃左右及1400℃左右,相差不大。与此对应的是3个样条中的杂质含量均小于2.0%;莫来石相的相对比例均大于35%。这说明,控制材料中的Fe2O3及K2O含量均小于2.0%,可以使材料的荷重软化温度保持在1400℃以上,且增加液固比对提高材料的起始软化温度影响不明显。
液固比从5:1继续降低至2.5:1时,起始软化温度从1400℃降至1320℃左右。与此对应,样条中的杂质Fe2O3含量从1.82%快速增加至5.32%,K2O的含量基本仍在2.0%左右;莫来石相的相对比例下降到29%。继续降低液固比使得材料中的Fe2O3含量的快速上升,荷重软化温度迅速下降80℃左右。
液固比从2.5:1降低至1:1时,起始软化温度1320℃左右。样条中的杂质Fe2O3含量大于10.0%,K2O稍大于2.0%;莫来石相降至1%左右。可以发现虽然继续增加液固比使材料中莫来石相近乎消失,Fe2O3含量液增加了1倍左右,但此时材料的高温性能并没有明显改变。因此,随着液固比的降低,材料杂质含量的增加,从高温使用性能的角度考虑控制液固比大于5:1,材料中的Fe2O3及K2O含量均小于2.0%,可以使材料的起始软化温度保持在1400℃以上,基本达到了NZ-45耐火砖的标准。
相比传统的粘土耐火砖,本文开发的利用铝土矿尾矿通过酸浸除杂烧结工艺制备的莫来石相耐火材料不仅在性能上达到了相应的行业标准要求,而且利用铝土矿尾矿替代粘土作为原料明显降低了生产成本,且环境效益显著。相比传统的烧结工艺,由于本文采用尾矿作为原料,因此增加了酸浸除杂工艺,虽然引入盐酸对环境有些影响,但本文研究了液固比和盐酸浓度对样条性能的影响,最大限度降低了盐酸的浓度和用量。酸浸除杂工艺也属于常见的工业除杂工艺,无需复杂设备和工序改造,利于工业推广。
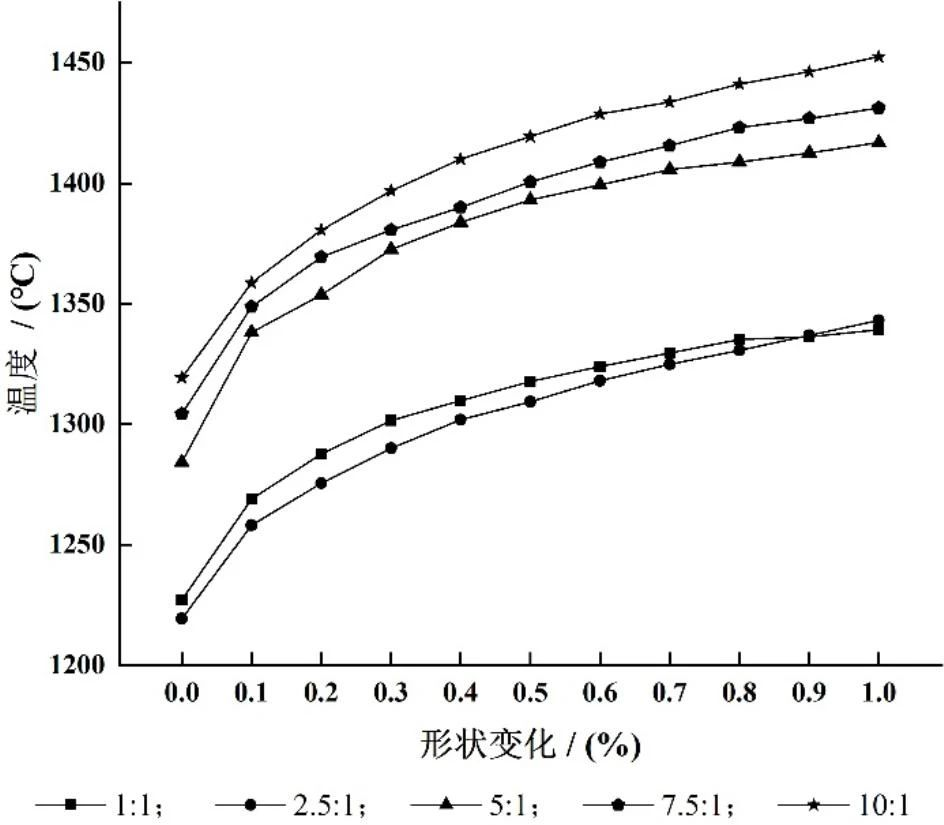
图10不同液固比的样条的荷重软化温度测试实验结果
3 结论
本文主要研究了不同酸浸条件下二元杂质Fe2O3及K2O成分对烧结制品的微观形貌、物相变化、常温力学性能以及高温性能,分析了酸浸条件对以上性能的影响规律,得出以下结论:
1)减少盐酸浓度或液固比对样条中的杂质K2O含量影响不大,但对Fe2O3影响较大。
2)当杂质Fe2O3与K2O含量均不大于2.0%时,材料的莫来石相对含量、荷重软化温度均较高、但材料常温力学性能低;当杂质Fe2O3与K2O的含量均在2.0%以上,材料的莫来石相对含量、荷重软化温度均较低、常温力学性能较高。
3)在K2O含量为2.0%左右的条件下,高杂质含量的Fe2O3小部分参与形成赤铁矿相,大部分参与形成非晶相,材料中非晶相含量的增加主要归因于材料中杂质Fe2O3含量的增加。
4)当材料中的Fe2O3及K2O的含量均小于2%时,可保证材料的荷重软化温度保持在1400℃以上,样条的荷重软化温度和常温力学性能都达到市售NZ-45耐火砖的标准。